

Maximum Stock Level = Reorder Level + Reorder Quantity – (Minimum Consumption x Minimum Reordering Period)įor example, if you know that when inventory touches 1000 units (reorder level), you must order 500 units (reorder quantity), and that your goods take at least 5 days to reach you from a vendor (minimum reordering period), and also that you sell a minimum of hundred units every day (minimum consumption), the maximum amount of stock that you need to keep in the inventory is a 1000 units. This number is influenced by several factors- the perishability of goods, the amount of warehouse space you have, changes in consumer preferences, etc. Maximum Stock LevelĪs the name implies, this is the level of stock indicated by a number beyond which you simply shouldn’t stock up on a particular product. Well, at least it may seem like jargon, but these terms that are casually thrown around in inventory management can help you understand better. Key Inventory Management Terms You Need To Know The fundamental principle of inventory management revolves around placing an order for goods at the right time, with the right source that can provide you with the right quantity at the right price and the right quality. Moreover, you can significantly reduce the time between order and delivery by having your own stock. When you buy in bulk, you also have an advantage when it comes to price negotiations. Having your own inventory helps hedge against the great uncertainty that is consumer behavior. Or your vendor may increase the price of a product you agreed to sell for way lesser. Is it not just simpler to ask a supplier to send you products as and when you have some demand for them? The issue, however, lies in the fact that we never know for sure what a customer’s spending pattern is.įor example, it is possible that your manufacturer cannot keep up when your demand peaks. You may have often wondered why you even have any inventory at all.
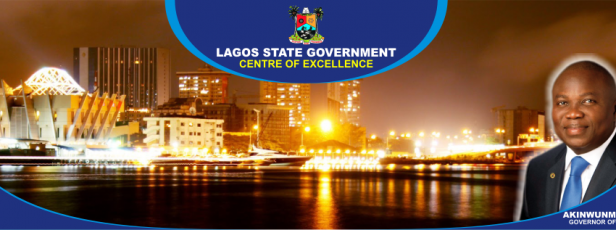
raw material: this includes all of the material that you will use to produce a certain product.In the manufacturing industry, inventory is divided into three major types for ease of accounting.
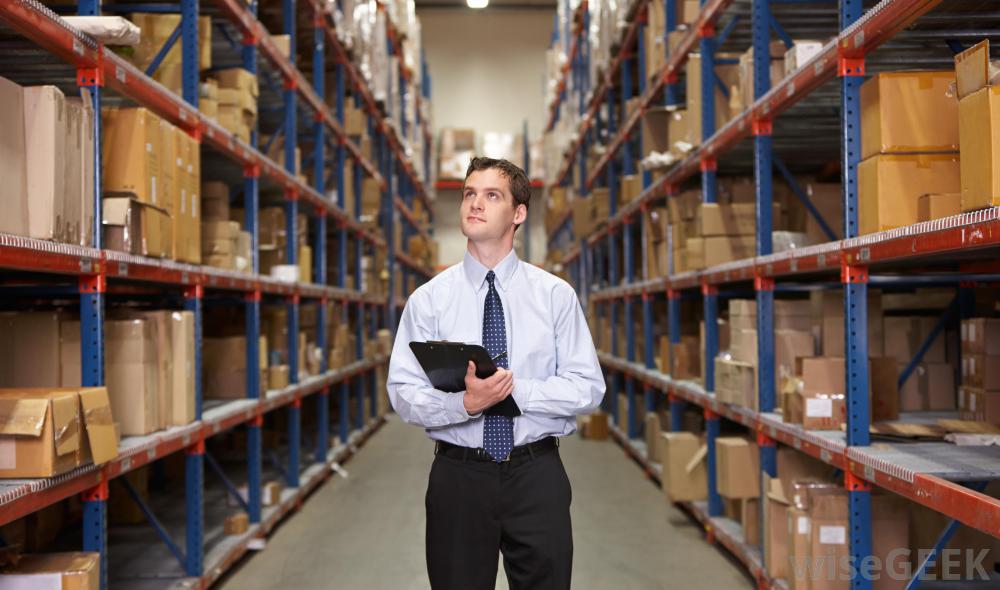
This is the product that is ready for a sale. What are the types of Inventory?įor a retailer, there is usually only one type of inventory. It is measured in units of stock as well as the value of the stock you hold.

In a retail context, very simply, Inventory refers to your raw material as well as the stock finished goods of products that you sell.
#AVERAGE SALARY FOR INVENTORY MANAGER SOFTWARE#
